Process Analysis of Silicon-Carbon Anode Materials Prepared by CVD Method
The common methods for preparing silicon-carbon anode materials include mechanical ball milling, spray drying, and chemical vapor deposition (CVD) method, etc.
The mechanical ball milling method crushes the bulk material into fine particles through the collision between the material and the rotating balls. The process is simple and the cost is low, but the phenomenon of particle agglomeration is severe. Moreover, excessive grinding will damage the crystallinity and surface of graphite, thereby causing secondary reactions.
The spray drying method involves using a heating gas to rapidly dry a liquid solution to produce dry powder. It is simple, continuous, and scalable.
CVD method is a process in which gaseous or vapor-like substances react at the gas phase or gas-solid interface to form solid deposits. This method has relatively low requirements for equipment, simple and controllable process, and can achieve high-quality deposition. At the same time, it has strong scalability and is easy for industrial production. The silicon-carbon anode materials prepared by the CVD method usually have high initial charge-discharge efficiency and good cycle stability, showing great development prospects.
It is reported that the ongoing projects of Ganzhou Litan New Energy Technology Co., Ltd. include the "Annual Production of 300 Tons of New Silicon-Carbon Negative Electrode Materials Project". This project intends to use the CVD method to prepare silicon-carbon negative electrode materials. The main process is as follows: feeding materials → activation → deposition of silicon → deposition of carbon → mixing → demagnetization → sieving → packaging.
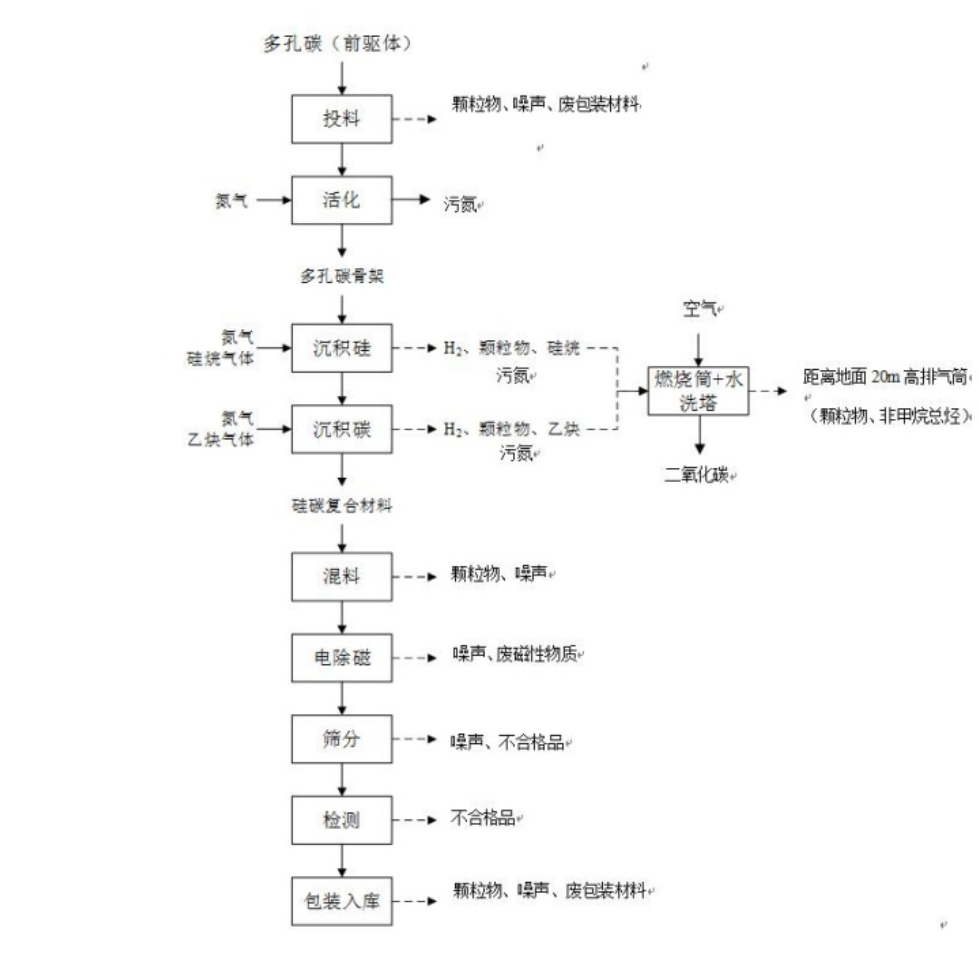
Incorporating materials: Using porous carbon raw material as the precursor, the porous carbon raw material is sent into the feeding system. The feeding system uses a negative pressure pumping method and transports it through a sealed pipeline to the reaction furnace in the next process for activation.
Activation: The feeding system uses a negative pressure pumping method to deliver the porous carbon into the reaction furnace through a sealed pipeline. Then, nitrogen gas is introduced into the reaction furnace for protection. The temperature is gradually raised to the activation temperature (800 - 1000℃) and maintained for 10 hours. Under nitrogen protection, the carbon undergoes an oxidation reaction to obtain the porous carbon framework.
Deposited silicon : After the activation reaction, a porous carbon framework material is obtained. It is then transported to the chemical vapor deposition furnace. Subsequently, nitrogen gas is introduced as a protective gas, and the temperature is gradually raised to the required deposition reaction temperature (400 - 800℃) for 5 - 10 hours of holding. During the nitrogen gas protection and holding period, silane gas is introduced into the high-temperature furnace for decomposition. The autoignition temperature of silane is 435℃. Most of the silane gas can self-ignite in the furnace without causing a large amount of leakage. The negative pressure cracking is ensured inside the furnace, and no explosion area is formed outside the high-temperature furnace. During the decomposition of silane, the porous carbon framework remains in the high-temperature furnace, and the silane gas undergoes high-temperature decomposition to generate nano-silicon. The nano-silicon particles deposit on the surface of the porous carbon framework and are embedded in the gaps of the porous carbon framework, achieving the deposition of silicon. After the deposition of silicon is completed, the silane is turned off. The chemical reaction equation involved in the deposition of silicon is: SiH4 → Si + 2H2↑.
Depositional carbon : After the deposition of silicon is completed, turn off the silane gas and maintain the nitrogen input and the required temperature for the deposition reaction (400 - 800℃) for 5 - 10 hours. Under the protection of nitrogen, introduce acetylene gas into the high-temperature furnace for decomposition. Acetylene decomposes into carbon at a temperature of 400 - 800℃, and the decomposed carbon deposits on the pores of the porous carbon material and coats the outer surface of the silicon. Finally, a high-capacity silicon-carbon composite material is obtained. After the deposition of carbon is completed, turn off the acetylene and only introduce nitrogen for cooling. Wait until the temperature drops to room temperature, then remove the material. The chemical reaction equation involved in the carbon deposition process is: C2H2 → 2C + H2↑.
Mixing materials: After the deposition of silicon is completed, the silicon-carbon composite material is sent through a sealed pipeline with negative pressure into the mixing machine. It is mixed evenly to enhance the uniformity of each batch. The mixing process lasts for about 1 hour under the high-speed rotation of the mixing machine to achieve a thorough mixing effect. The mixing machine is fully enclosed, and no dust is generated during the transportation and mixing process. Only a small amount of dust from material feeding will be produced when the material enters the feeding area for feeding, and it will be collected, treated, and discharged together with the dust exhaust from the feeding process.
Demagnetization : Considering that there might be a small amount of magnetic substances such as iron in the raw materials, the presence of these magnetic substances will seriously deteriorate the cycle performance and safety performance of lithium-ion batteries. Therefore, the prepared silicon-carbon composite material needs to undergo magnetic removal treatment, and thus it needs to be processed by a magnetic separator in the magnetic removal machine. The mixed materials are conveyed to the demagnetization machine through the pneumatic conveying system for demagnetization treatment. The magnetic substances in the materials are affected by the magnetic field and will be adsorbed onto the equipment. When the magnetic substances accumulate to a certain amount, they are discharged through a separate outlet. Demagnetization refers to generating a magnetic field through current transformers. The magnetic field strength is ≤ 5000 gauss, which will not cause environmental impact or harm to employees' bodies. The generated magnetic field is used to adsorb the magnetic substances contained in the negative electrode materials, thereby achieving the purpose of demagnetization. The feeding and discharging of the demagnetization machine adopt sealed pipeline pneumatic conveying, so the demagnetization process will hardly produce dust, and mainly generates waste magnetic substances, etc.
Screening : The magnetically treated materials are conveyed by pneumatic means through sealed pipelines and sent to the vibrating screen for screening, thereby removing the large particles from the materials.
Testing: The qualified materials are sampled for testing. If the products fail the test, they will be disposed of together with the materials from the screening process that are also unqualified.
Packaging storage: The products that pass the inspection are sent to the automatic packaging system. The sealing machine is used to seal and pack them. The materials flow directly through the pipeline into the packaging bags, achieving a sealed packaging.
RELATED POSTS
Lithium Carbonate Hits Rare Price Limit Up! Has Industry Restructuring Concluded?